Seacow Ballast Hoppers
Background.
Nick C writes about the problem of ballast deployment on the NYMR, resulting in the purchase and refurbishment of Seacow ballast hoppers.
In 2012, the P. Way Department found itself with a bit of a problem, regarding ballast lifting capability.
At that time, the ballast train comprised two 1947 built WALRUS 40T capacity bogie wagons, a 25T capacity DOGFISH four- wheel wagon and five 21T capacity coal hoppers. The coal hoppers had been slightly modified to regulate the flow of ballast, though not to the same standard of accuracy that could be delivered by ballast wagons specifically designed for the purpose.
The two WALRUS wagons were giving serious concern as the poor-quality post war steel used in their construction, was corroding badly. As a result, the doors on one were no longer capable of opening. The doors on the other wagon were little better. The main load bearing frames were badly corroding as well.
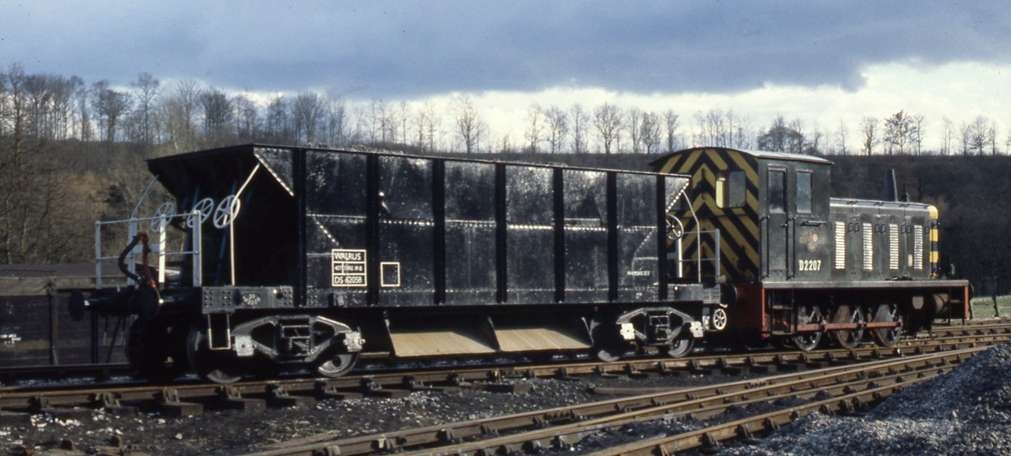
WALRUS wagon DS62058 in better times in the early 1980s
Assessment.
Putting the work of rebuilding out to a contractor was considered, as this work was beyond our capability. The integral nature of their construction unfortunately precluded doing this at any reasonable cost.
We then started looking around for possible replacements. Fortunately, at that time, EWS at Doncaster had an air braked 1973 built Seacow ballast wagon, on an isolated siding, that was in the way of a major depot rebuilding. They wanted rid of it in a hurry and we were delighted to take it off their hands.
Shortly after purchasing this Seacow wagon, T.J Thompson at Stockton announced that they were in the process of clearing their scrapyard. They had a fleet of Seacow ballast wagons in stock at a reasonable price and, most importantly, were quite happy to take our condemned wagons in part exchange.
A detailed inspection by the NYMR Wagon Group wagon professionals revealed that four of them were in reasonably good order. One, a Sealion, had not had its vacuum brake gear removed, so it was still dual braked. These were duly acquired, being dispatched by road to New Bridge in June 2014.
The lorries involved returned to Thompsons with the two WALRUS wagons and a 1947 built BORAIL wagon, that had similar major corrosion problems.
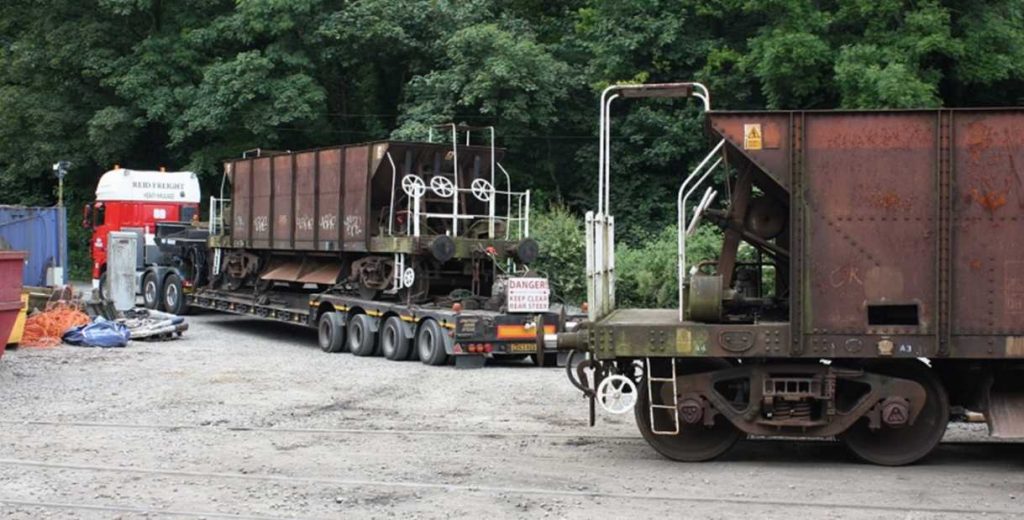
Seacow arrival at New Bridge, from Thompsons scrapyard.
Brakes.
We now had the potential for running either a full air braked ballast train, or a shorter length vacuum braked train, utilising only the Sealion and the vacuum braked Dogfish.
The master plan also envisaged fitting the Dogfish with a through air pipe and the Shark ballast brake the same, with the addition of an air pressure gauge in the cabin. It is fortunate that the NYMR diesel fleet includes at least two main line locomotives that are air braked. These are quite capable of powering a fully laden ballast train, which is the equivalent of a ten- coach passenger set.
The 21T coal hoppers were earmarked for progressive withdrawal once their air braked replacements had been overhauled.
The one sticking point in this plan though, was that we had no experience of refurbishing or servicing air braking systems, as all our previous work had been with vacuum brakes.
‘Cometh the hour, cometh the man’ the saying goes, and in this respect, we were very fortunate.
Richard Kimber, former depot engineer at Leeds Neville Hill and an expert on air brakes had just joined the department following retirement, and was looking for something meaningful to do. He could not have come at a better time or to a better place!
Seacow Refurbishment begins.
Seacow DB982667, the Doncaster purchase, became the first example to be brought into the workshops for overhaul. Whilst Richard got on with stripping the air brake equipment and brake rigging, the rest of the team got on with needle gunning everywhere and cutting out and replacing a considerable amount of hopper plate work – one of the reason the wagon had been condemned in the first place.
Another reason for withdrawal, was the parlous state of the skins of the rotating curved hopper doors. These were rather like paper lace. The frames of the doors were little better. Only the castings on the ends which held the door rotation pins were suitable for retention.
The pins proved a real problem to undo. They are held in place by very large nuts, which, due to poor lubrication in the past, had seized solid. Some came out after copious heating with a torch and much brute force, which often involving splitting the castellated nuts. Some did not and had to be gas axed.
The York Area Group.
The York Area Group paid for some specialist round bar and the machine shop at the MPD. Using a good one as a pattern, they made as a few spare sets of pins and nuts, which hopefully will suffice for the whole refurbishment programme.
Even with the pins out, the doors themselves proved difficult to physically get out of the wagon. The centre ones were the easiest as they could be dropped straight out the bottom. The side doors had to be rotated through 180 degrees and slid down the chutes, with no more than a millimetre or two to spare. If the lowering was anything less than square, the chute rivets often got in the way, causing jamming.
We appointed a local agricultural contractor to re-skin the doors. As it turned out, the necessary replacement of the entire longitudinal frame of each one in the process. This was done to a fine tolerance, being just as well, as the design required a very tight fit in both the wagon frame housing, and in lifting the new doors back up the chutes in the first place.
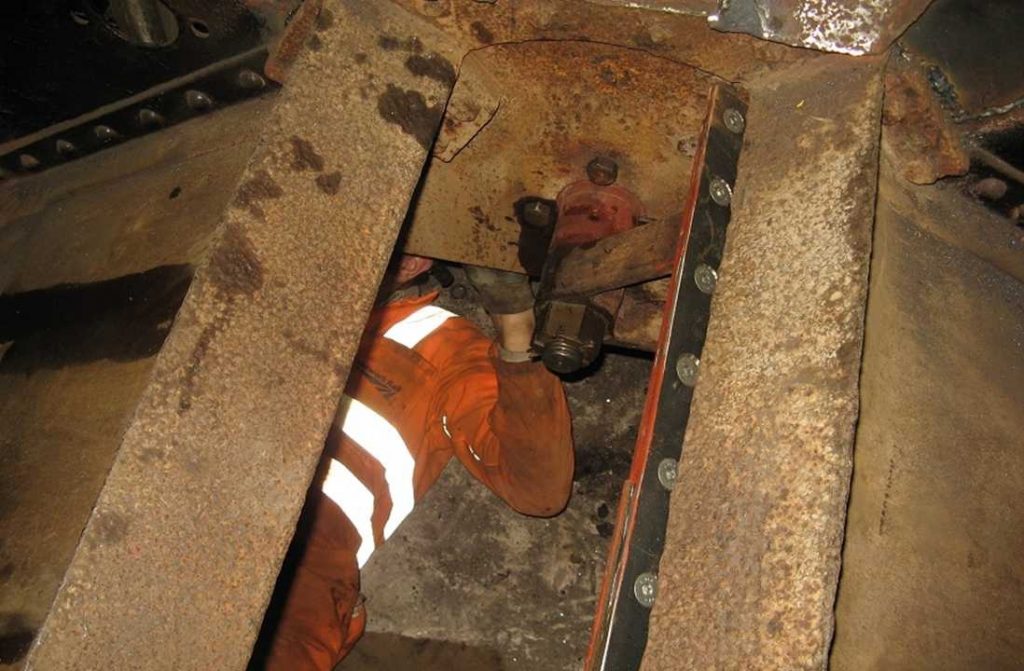
Looking down on the edge of the new Seacow door. Note the new rotation pin and castellated nut.
Testing times.
The air brake reservoir went to the MPD for pressure testing along with the air brake cylinder. The Westinghouse P4 distributor, the ‘brains’ of the braking system, was despatched to Railway Brake Services at Doncaster. Furthermore, two identical P4s, one from the air braked RUDD spoil wagon and the third, a planned rotational spare. This has subsequently been fitted to the Plasser 12T hydraulic crane.
The obvious question then arose, as to how we could test the braking system, once all the parts were re-assembled.
Richard suggested the construction of a test cart, capable of replicating the action of a locomotive braking system. Thoughts then turned as to how we could achieve this.
Once again serendipity set in. Traction Inspector and NYMHR Trust vice chairman, Chris Cubitt, happened to be passing by New Bridge depot. Upon asking on progress, revealed that an air brake test cart, or rather the vandalised hulk of one was available. This was sitting in the undergrowth on the Bellwood site at Grosmont. More importantly, as it had been there many years with no progress, it was ours for the asking.
Once we brought it back to New Bridge, what remained of the broken components were removed. The hulk was stripped back to bare metal, the cracked frame welded up and a missing handle fabricated. The only salvageable item of equipment from the rig, was the long flexible air brake hose for coupling to wagons.
Completed Test Cart.
Following painting up in high visibility bright yellow paint, a brand-new lorry air reservoir was fitted underneath. This was connected up to a spare air brake controller from our stores. On the top were fitted a train pipe gauge, brake cylinder pressure gauge and auxiliary reservoir gauge with flexible connections. This enabled these items to connect into the relevant parts on the wagon, to enable monitoring under test. For completion an air supply gauge was also fitted with regulator and all the gauges covered in protective mesh screens.
The whole rig receives its air supply from the depot portable compressor. Richard has designed and produced a full set of test documentation for both the wagon and the test cart itself.
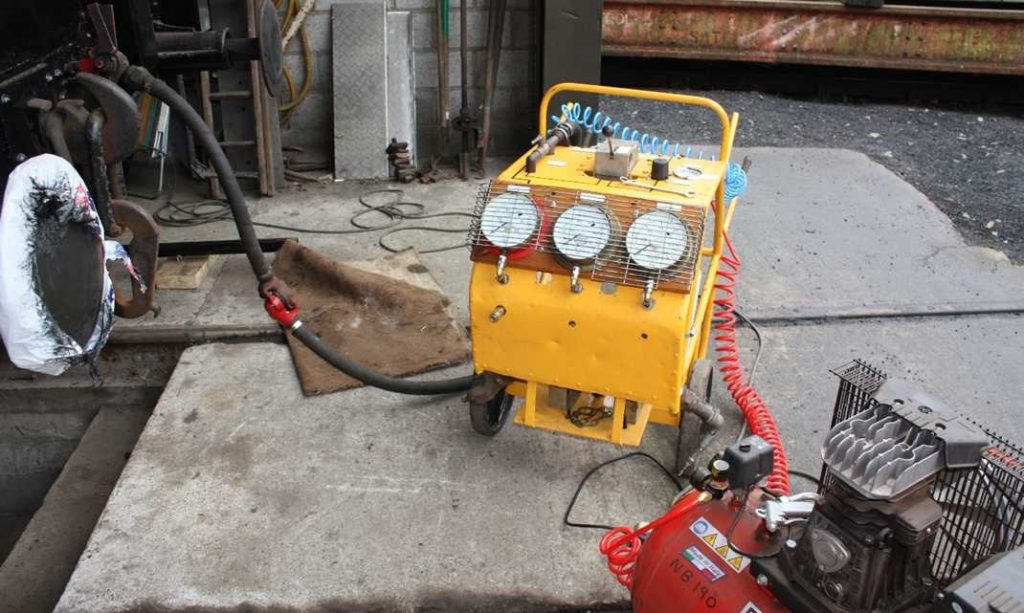
Air brake test cart in use, powered by the adjacent air compressor.